In today’s competitive manufacturing landscape, finding ways to improve efficiency and save costs is crucial for the success of fabrication shops, especially those heavily reliant on manual welding machines. While investing in automated welding systems may come with an initial cost, the long-term benefits they offer can significantly impact your bottom line. In this blog post, we will explore the advantages of automated welding and why making the switch can revolutionize your welding operations, allowing you to do more welds in less time, with fewer skilled welders.
Increased Efficiency and Productivity:
Automated welding machines, including semi-automated welding systems, streamline the welding process and eliminate the need for manual intervention. By leveraging advanced technology and precision controls, these machines can perform welds consistently and with high accuracy. This results in increased efficiency, faster production cycles, and reduced idle time, ultimately boosting overall productivity.
Cost Savings on Skilled Labor:
One of the most significant expenses for manual welding shops is the cost of skilled welders. However, with automated welding systems, you can optimize your workforce by relying on fewer highly skilled welders. These machines handle complex welds with minimal human intervention, reducing the dependency on manual labor and mitigating the risks associated with human error. Consequently, this leads to substantial cost savings on labor expenses in the long run.
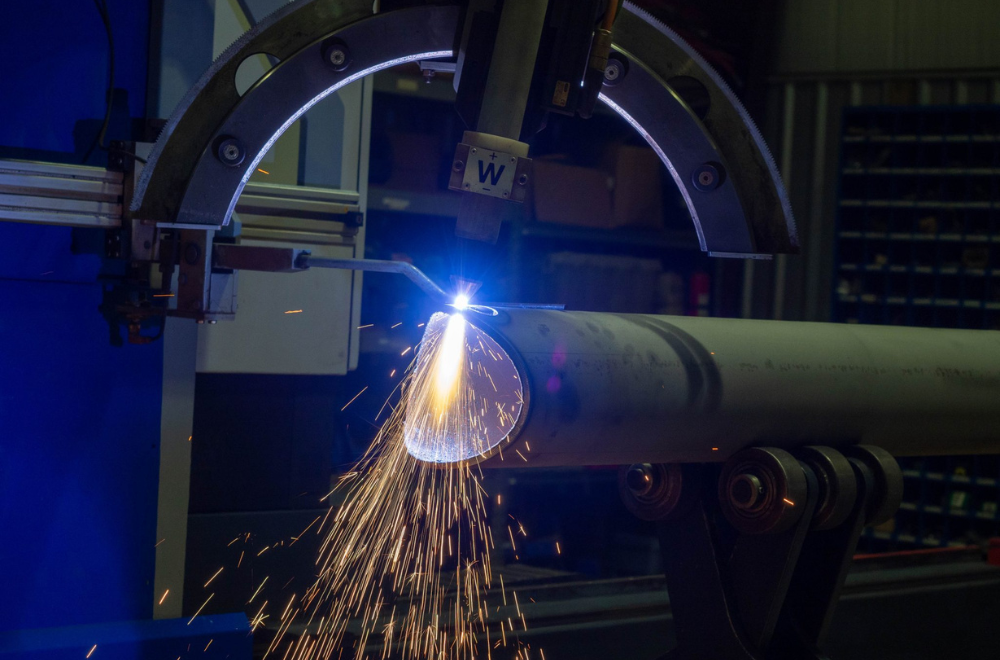
Consistent Weld Quality:
Automated welding machines offer unparalleled precision and repeatability, ensuring consistent weld quality throughout the production process. By eliminating human variability, these systems reduce the chances of defects, rework, and material wastage. The result is a significant improvement in weld quality, reducing the need for costly touch-ups and enhancing the overall reliability and durability of your welded components.
Faster Project Turnaround:
Manual welding processes often have limitations in terms of speed and throughput. However, automated welding systems excel in fast and efficient weld completion. By increasing the welding speed and reducing cycle times, these machines enable faster project turnaround. This allows you to take on more projects within the same timeframe, expanding your capacity and generating increased revenue for your fabrication shop.
Improved Workplace Safety:
Safety is of paramount importance in any welding operation. Automated welding machines help mitigate safety risks by reducing the need for welders to be in close proximity to hazardous welding processes. With advanced safety features, including remote operation and monitoring capabilities, these systems create a safer working environment for your employees, reducing the potential for accidents and associated costs.
Investing in automated welding systems and semi-automated welding machines, can be a game-changer for manual welding shops. Despite the initial cost, the long-term benefits in terms of increased efficiency, cost savings on skilled labor, consistent weld quality, faster project turnaround, and improved workplace safety make it a worthwhile investment. Embracing automation in your welding operations will not only optimize your bottom line but also position your fabrication shop for greater success in today’s competitive market.